What is the Drum rotary screen for sugar mill
July 17, 2023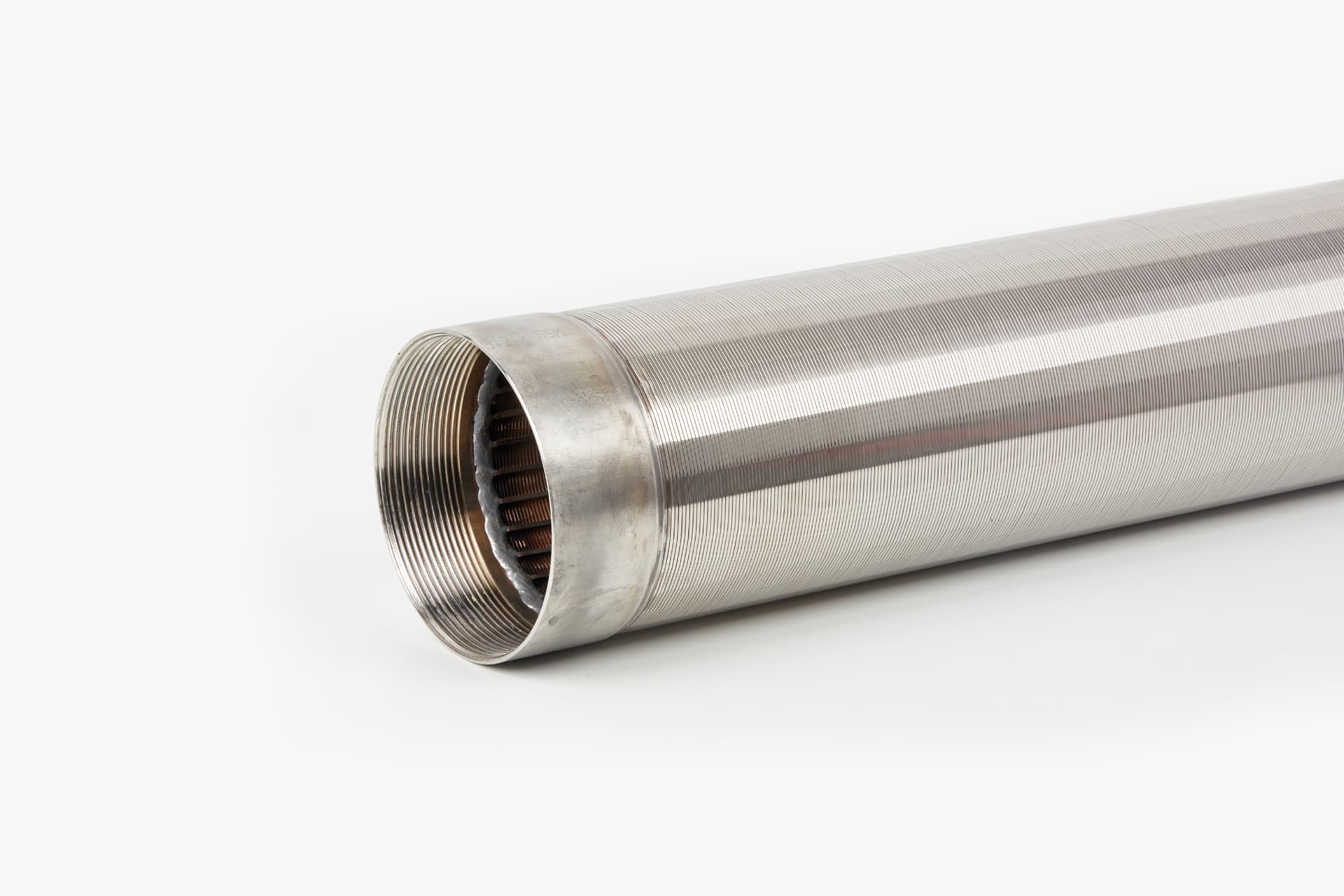
Johnson Stainless Steel Well Screens
September 5, 2023Wedge Wire Screens and Perforated Screens are two commonly used types of screening media in various industries. They have different structures, design characteristics, and uses.
Wedge Wire Screens
Wedge wire screens, also known as profile wire screens, consist of a series of shaped wires known as profiles that are welded onto support rods. This produces a slot opening that can be adjusted according to the needs of the application.
Advantages:
- Non-Clogging: The V-shaped wire design ensures non-clogging operation, which is crucial for applications involving liquids and fine particles.
- High Strength: The welding process provides high strength and rigidity.
- Customizable: The slot size, wire shape, and rod spacing can be customized according to application needs.
- High Open Area: They often provide a higher open area compared to perforated screens, which can result in higher flow rates.
Perforated Screens
Perforated screens are sheets of material such as steel, stainless steel, or plastic that have been punched with holes in a pattern or in a specific arrangement.
Advantages:
- Versatile: They can be used in a diverse range of applications due to the wide variety of hole sizes, shapes, and patterns available.
- Durability: Depending on the material used, they can offer high durability and resistance to corrosive environments.
- Economical: They are generally less expensive to manufacture than wedge wire screens.
Key Differences
The key differences between wedge wire screens and perforated screens are:
- Structure: Wedge wire screens are made of V-shaped wires welded to support rods, while perforated screens are sheets of material with holes punched in them.
- Clogging: Wedge wire screens are less likely to clog due to their V-shaped wire design, while perforated screens may be more susceptible to clogging.
- Customization: Wedge wire screens offer more customization options in terms of slot size and wire shape, while perforated screens offer more choices in terms of hole size and pattern.
- Cost: Perforated screens are generally less expensive to manufacture than wedge wire screens.
- Flow Rate: Wedge wire screens often offer higher flow rates due to their higher open area compared to perforated screens.
Remember, the decision to use a wedge wire screen or a perforated screen will depend on the specific requirements of your application.