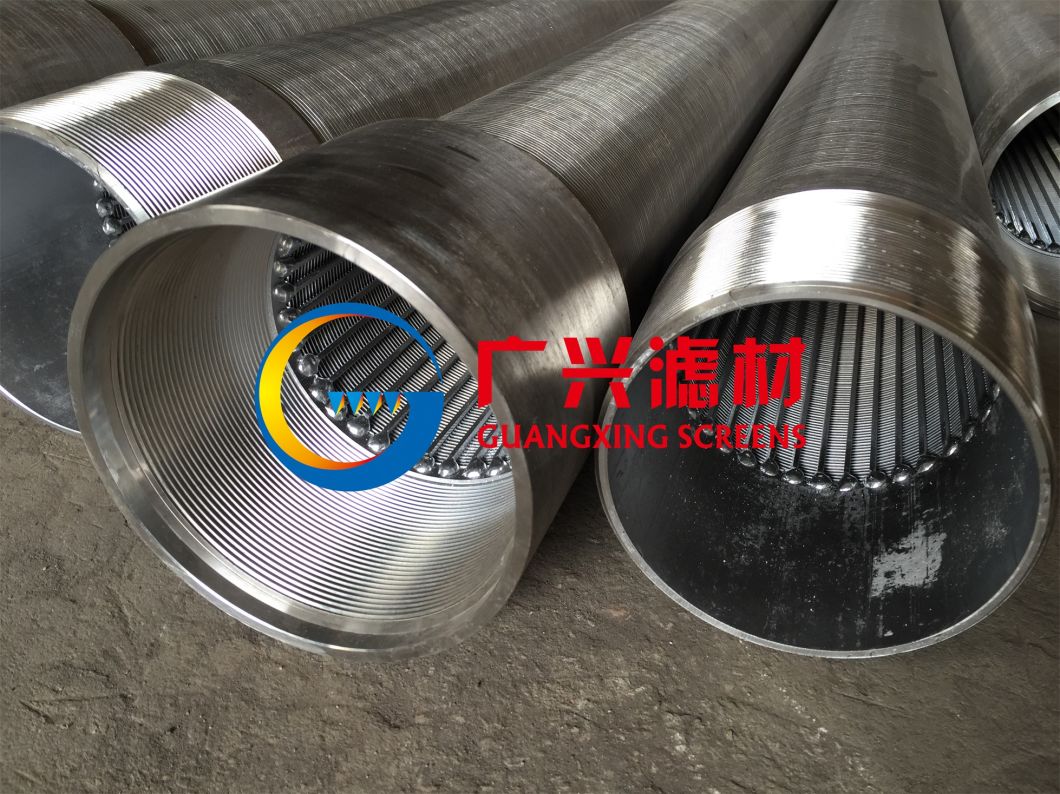
What are applications of the Johnson well Screen ?
September 5, 2023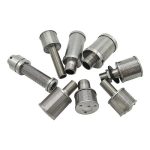
Wedge Wire Screen Filter Nozzle
September 30, 2023Introduction
The importance of well screens in water extraction and oil and gas production applications cannot be overstated. Serving as the first line of defense against sand and sediments, well screens play a pivotal role in maintaining the efficiency and longevity of a well. Among the various materials used in manufacturing well screens, stainless steel stands as the most preferred due to its superior mechanical properties and corrosion resistance. This essay undertakes a comprehensive dynamic study of common stainless steel materials used in well screens, focusing on their performance under different operational and environmental conditions.
Stainless Steel Mesh Screen Specifications:
We offer general filtration and heavy duty metal mesh screens for filtration and separation applications in Water, Oil / Gas, Geothermal, Petrochemical, General Filtration Industries and Environmental Monitoring.
Materials: Grades of simple stainless steel 304, 316, 304L right up to highly corrosion resistant alloys.
Slot opening: Slot should be bigger than 0.020mm and less that 2500mm long.
Wire shapes and sizes: Custom
Combination of wire and rods: Available to meet the open area and strength requirements for the particular application.
Technical data of 304 316Lstainless steel wedge wire screen
No. | (mm)TYPE | OD (mm) | ID (mm) | Support wire Number | Filter direction |
1 | SRD25.4 | 25.4 | 18.6 | 12 | FOTI |
2 | SRD 33 | 33 | 24 | 8 | FOTI |
3 | SRD 37 | 37 | 28 | 8 | FOTI |
4 | SRD 40 | 40 | 31 | 8/10 | FOTI/FITO |
5 | SRD 45 | 45 | 36 | 10/12 | FOTI/FITO |
6 | SRD 48 | 48 | 38 | 12 | FOTI/FITO |
7 | SRD 60 | 60 | 51 | 12 | FOTI/FITO |
8 | SRD 70 | 70 | 61 | 12/18 | FOTI/FITO |
9 | SRD 85 | 85 | 76 | 18 | FOTI/FITO |
10 | SRD 110 | 110 | 101 | 24 | FOTI/FITO |
11 | SRD120 | 120 | 111 | 24 | FOTI/FITO |
Stainless Steel Profile Wire Well Screen Constructed with Continuous Slot Opening and Large Open Area, Providing Greater Water In-taking Efficiency
Non Clogging V Wire Pipe Base Screen ensures an uninterrupted free flow and an effective sand control.
Stainless Steel: An Overview
Stainless steel, an alloy of iron, carbon, and a minimum of 10.5% chromium, is renowned for its remarkable resistance to corrosion. The chromium in stainless steel forms a thin passive layer of chromium oxide on the surface, which prevents further surface corrosion and blocks corrosion from spreading into the metal’s internal structure. In well screen applications, where the material is continually exposed to a harsh, corrosive environment, this corrosion resistance is of paramount importance.
Grade 304 Stainless Steel
Stainless steel 304, often referred to as ‘A2′ or ’18/8′ stainless (due to its 18% chromium and 8% nickel content), is the most common grade of stainless steel. It offers excellent corrosion resistance in most environments and possesses good mechanical properties. However, its Achilles’ heel lies in environments with high chloride content, where its performance can be compromised, leading to pitting and crevice corrosion.
Despite this, the 304-grade remains a popular choice for well screens due to its balance of corrosion resistance, availability, and cost. It is particularly well-suited for use in freshwater wells, where chloride levels are typically low.
Grade 316 Stainless Steel
For environments where the corrosion resistance of 304-grade stainless steel is insufficient, 316-grade stainless steel, also known as ‘A4’ or ‘marine grade stainless’, comes into play. The addition of 2-3% molybdenum increases its resilience against chloride attack, offering higher resistance to pitting and crevice corrosion.
The 316-grade, therefore, finds its use in well screens for saltwater wells or in regions where the soil has high salinity. It also provides a higher degree of resistance against solutions of sulfuric, phosphoric, and acetic acids.
Grade 316L Stainless Steel
Grade 316L is a low carbon version of grade 316. While it offers similar corrosion resistance, the lower carbon content provides improved weldability and heightened resistance to intergranular corrosion following welding or heat treatment. This makes it an ideal choice for well screens in applications requiring extensive welding.
Duplex Stainless Steel
Duplex stainless steels, such as grade 2205, provide an interesting alternative to traditional austenitic stainless steels. These alloys blend the beneficial properties of austenitic and ferritic stainless steels, offering enhanced strength and improved resistance to stress corrosion cracking.
Duplex stainless steels are becoming increasingly popular for use in well screens in demanding applications where high strength and superior corrosion resistance are critical.
Comparative Analysis
While all these materials provide excellent corrosion resistance, their performance can vary significantly under different environmental conditions. Factors such as pH levels, temperature changes, and chloride content can dramatically affect their corrosion behavior.
For instance, while grades 304 and 316 show similar corrosion resistance in neutral and mildly acidic conditions, grade 316 significantly outperforms grade 304 in more acidic or high chloride environments. Similarly, while duplex stainless steel shows excellent corrosion resistance in a wide range of conditions, it can be susceptible to pitting and crevice corrosion in environments with very high chloride levels.
Furthermore, mechanical properties such as tensile strength, yield strength, and hardness also play a critical role in determining the suitability of a material for well screen applications. These properties can be influenced by factors like heat treatment and the presence of other alloying elements.
Conclusion
In conclusion, the choice of stainless steel grade for well screens depends on a balance of factors, including corrosion resistance, mechanical properties, the specific environmental conditions, and cost. By understanding how different stainless steel grades behave under varying conditions, we can make more informed decisions in selecting the most suitable material for well screen applications. This not only ensures the efficiency and longevity of the well but also contributes to cost savings and resource optimization.
By dynamically studying the common stainless steel materials used in well screens, we can pave the way for developing more efficient and sustainable extraction practices, shaping the future of the water extraction and oil and gas industries.