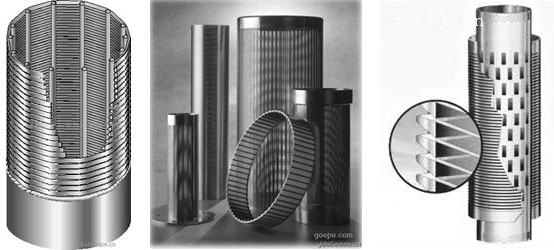
What‘s the difference between wire wrapped screen and Slotted Casing Pipe?
January 31, 2018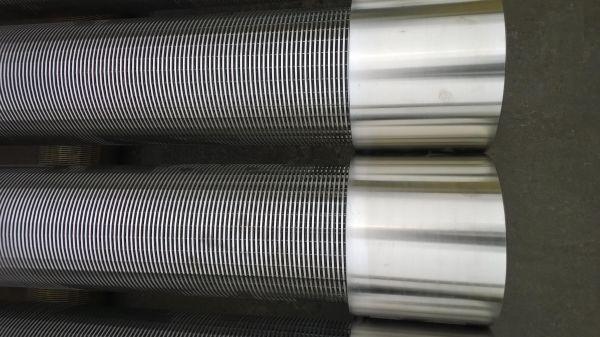
How to calculate strength of Wire Wrapped Screen filter on pressure
February 4, 2018Oil Sand control Screen _ PIPE Basic Sand Control well screen
In the oil drilling and production operation, the oil sand control screen is an important equipment, often used in advance completion or oil production sand control. At present, the use of a larger screen is a winding screen. This screen is manufactured by winding a section of steel wire on a metal liner evenly distributed around a sieve bar or opening and leaving a certain gap as a sieve hole.
Although this method of manufacturing has been used by many manufacturers in China, however, there are some problems in the downhole screen, especially when the pressure passes through the curved section of the high deviated well or the horizontal well, it is unavoidable to collide, squeeze and rub with the wellbore or casing, it is easy to appear the phenomenon of disorderly silk, causing the screen damage or gap deformation, Cause the completion quality and sand control effect to reduce or failure, for winding screen tube of this disadvantage, pipe, seam one of the slit screen appeared.
Because of the superior performance and low price of the slit pipe, it has been highly valued and widely adopted by the major oilfields. It can be seen that the appearance of slit pipe is the development of horizontal well and side drilling and the material condition of high sand oil reservoir.
The oil screen is a thousands of-strip slit which is distributed according to a certain regularity in the high-strength alloy copper casing. Commonly used gap specifications are: seam width 0.15-3mm, gap length 50-300mm; the oil slit screen is irradiated by a focused high power density laser beam on a screen, and the laser power density exceeds the laser threshold, and the energy of the beam and the working gas assist in cutting the chemical energy to be absorbed by the material, which causes the laser to be in the casing.
The temperature of the surface hot spot heats up rapidly, the working material melts or gasification to form the hole, when the casing and the laser beam relative movement, can then cut out the seam on the casing.